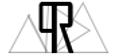
RIDHAM
PATEL
C F D & F E A
Bicycle Fork Aerodynamic
Developing Models w/ Design Constraints


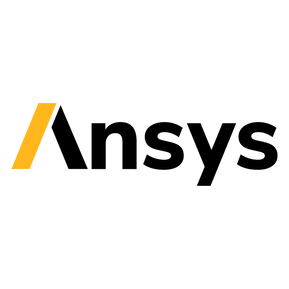
Project Objective
The design challenge of the given design project was to develop a front bicycle fork to reduce weight, increase stiffness and reduce aerodynamic drag of the object. This was done because aerodynamic drag from the combination of the bike and rider account for more than 90% of the total resistive forces felt. Therefore, by reducing the mass, drag coefficient and increasing stiffness 90% of the total forces would be tackled. Since, the design of racing bicycles conforms to strict design rules set by Union Cyclist International, this design project also had many geometrical constraints. These geometrical constraints were a part of the design challenge. There were also many design requirements such as the forces added onto the bicycle fork and maximum allowable displacements in each direction.
The design project was developed to tackle real life scenarios faced by many mechanical engineers in the field. Designs processes are usually iterative and take many tries to complete. Therefore, this design problem was a great way to kick-start what would be faced as mechanical engineers in the future. Particularly in this design project, three design iterations were taken. The first one being the most basic whereas the third and last one being the most complex. Design iterations were made from knowledge developed in engineering courses about points of highest deflection and fluid flow around a rigid body. With these two major design parameters in mind, the best possible solution was set as a goal to accomplish. From the first two iteration, it was known what mistakes were made and where these mistakes could be improved. This knowledge was then used to make the last iteration that performed the best from all the iterations. The last iteration had the highest stiffness factor while also having the lowest deflection, drag force and drag coefficient. The mass of the last iteration was also relatively low compared to all iterations except for design iteration two, which did not meet the criteria. The final iteration was also rounded off by adding various fillets to allow the fluid to flow smoothly around the rigid body. The design criteria was met and all the displacements caused by external loads added were under the requirements. This was all done while also reducing the drag force, drag coefficient and weight of the bicycle front fork. Final project report can be found below.