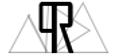
RIDHAM
PATEL
C A P S T O N E P R O J E C T
Human Powered Vehicle
American Society of Mechanical Engineer

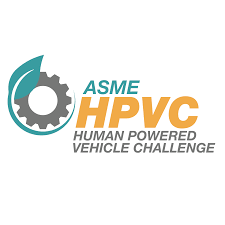

Project Objective
The Project was developed by Professor Hanson of York University to engage students to develop on designs that have been prominently around for a long time. The bicycle was first invented in 1817 and has come a long way through design iterations to it's current state. As pollution increases on our planet, the society as a whole needs to develop new ways to slowly counter act this notable problem. Through this capstone project, my team and I wanted to develop a HPV (human powered vehicle) that could not only compete in sports related activities but, could also be used as a means of getting around in densely populated areas such as downtown.
Initial Design
To initialize this project the team came together and created parameters and requirements that we needed to achieve by developing this capstone project. This was done with the assistance of our capstone supervisor Professor Ronald Hanson to insure that the vision of this project was fully captured. After developing a requirements list, measurements of each team member were recorded to insure that the minimum and maximum of each parameter could ride this vehicle without a problem. Through this we were able to insure that an averaged sized human being from the sizes of 4'10" - 6'7" could ride this vehicle. From this information i was able to actualize designs and ideas brought together by the team, into a 1:1 scale human powered vehicle frame shown below.



Design Iterations
After developing the first model, the model was tested on Star CCM for strength, durability and deflection. From the image above, it was evident that the frame was over designed. There were many additional, joints, beams and connections that were not needed for the purposes our team had sought out for. Through many calculations we had anticipated for a maximum deflection of 3mm at all joints and the frame was not anywhere close to this number in the x,y or z direction. Therefore, the frame was redesigned many times until, the lightest weight was achieved with a conservative deflection. This frame is shown below.
Final Solidworks Model

Capstone Stakeholder Final Presenation
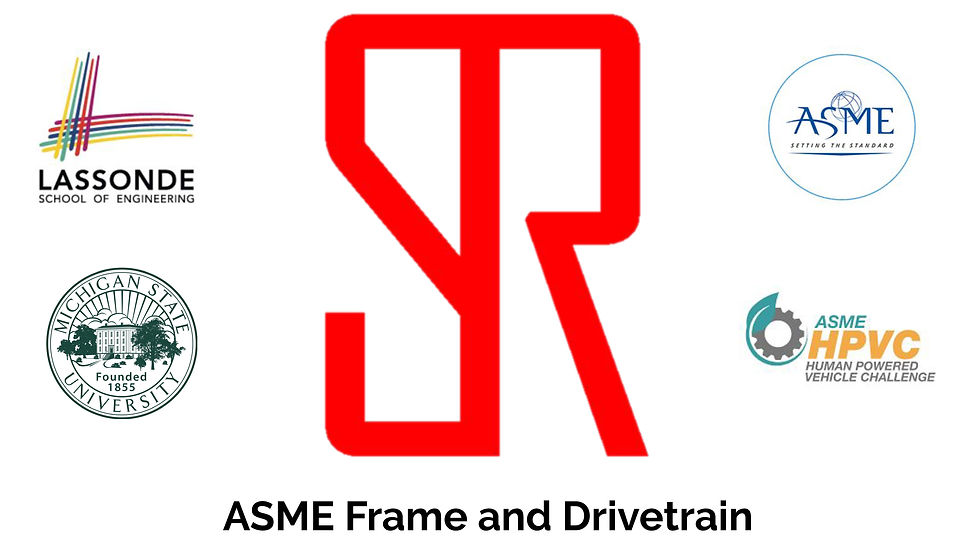
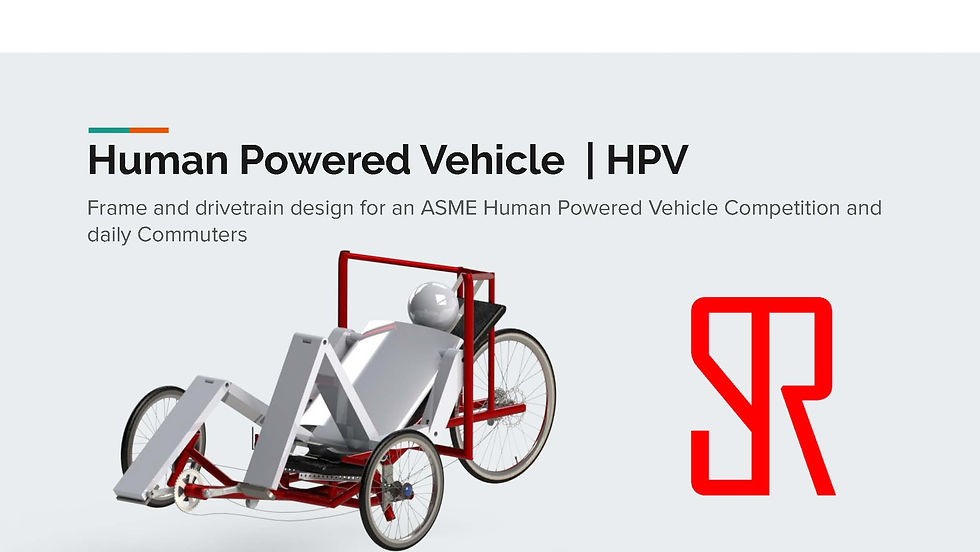

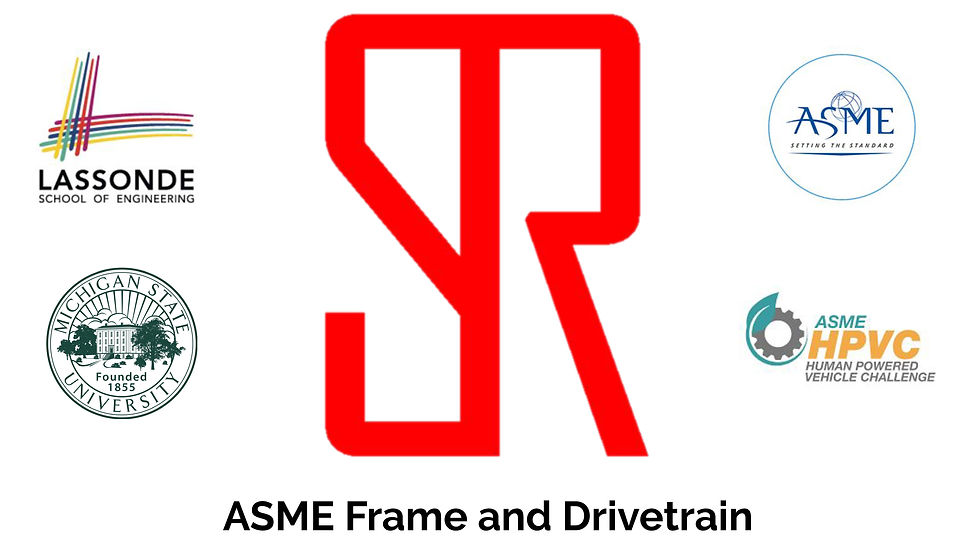